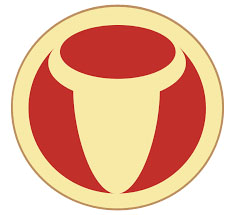
At Slonim meat processing plant a system for technological process automation was developed based on the 1C:CPM for Belarus solution. This was the first automation project in the meat processing industry of Belarus. As a result, the developed information system allowed for the surplus warehouse reduction by 20%, daily operational cost decrease by 20%, as well as labour cost reduction by 30%.
Slonim meat processing plant is one of the leaders in the meat processing industry of Belarus. It holds the 3d place for the production volume in the country. Its range of products includes up to 300 different kinds of meat products and the enterprise's output is about 500 tons of articles per day.
Before the project start, there were 12 unrelated systems at the enterprise, as well as duplicated data input operations, too slow reporting process, and, consequently, almost complete lack of operational analysis.
Project goal: enhance the plant’s efficiency by unifying disparate programs into a single information system for managing the company.
Project tasks
-
reduce the cost of products by decreasing and optimizing warehouse stocks;
-
accelerate operational reporting;
-
reduce labour costs.
Solution architecture
The technological process automation system is developed on the 1C:CPM for Belarus solution. The implementation was based on a traceability technology with the use of a bar coding system which allows getting information on any of the production cycles.
The following stages were implemented in the framework of the project:
1. Stocks accounting automation. The project team developed an application for the efficient delivery of raw materials to production taking into account expiration dates.
2. Pre-slaughtering cattle care and slaughtering shopfloor automation.
3. Laboratory. They also created a module for laboratory research accounting.
4. Refrigerated processing. Automated operations of raw material acceptance and delivery to the shop floor taking into account the specificity of working in low-temperature conditions.
5. Integrated production automation.
6. Product output. Ensured technological equipment synchronization for packaging and labeling.
7. Retail. The project executors developed an individual module that ensures accounting for all retail operations directly in the software according to the legislation of the Republic of Belarus.
8. Sales. A special logistics path was implemented for the efficient sale of finished goods including for export operations.
9. Bookkeeping. The implementation of corresponding stages was complemented with accounting automation in the software.
Project results
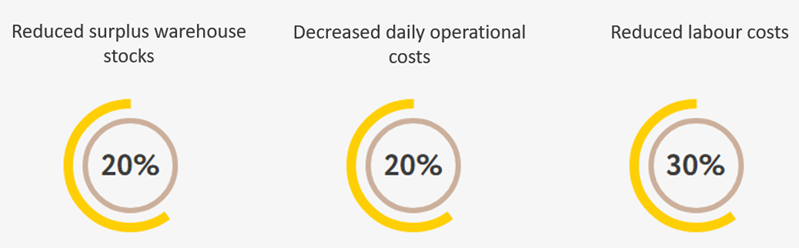
Implemented 1C:CPM for Belarus, fast data reception for reporting and analytics, accelerated and simplified automated production processes improved the overall production capacity and increased the enterprise’s potential. Nowadays, the Slonim meat processing plant penetrates new markets.
It’s worth mentioning the economic effect:
-
4 times faster production report generation;
-
9,5 times faster export report generation;
-
2 times faster accounting for retail operations;
-
Surplus warehouse stocks were reduced by 20%;
-
Daily operational costs decreased by 20%;
-
Labour costs were cut by 30%.
This implementation project became possible thanks to well-coordinated interaction between specialists of EtiketService, the leading 1C:Franchisee company in the field of implementing solutions based on the 1C:Enterprise platform in Belarus, and the IT-team of Slonim plant. Rapid managerial decision making, high engagement and motivation helped successfully finish such a grand-scale project.