Pioneering Automation and Efficiency with 1C:ERP at BIG Climatic Manufactory
BIG Climatic Manufactory, a leading name in climate equipment manufacturing in China, embarked on a strategic transformation to automate its operations using the 1C:ERP system. Partnering with Raytec DTG, a certified 1C implementation provider, the company set out to enhance operational efficiency, streamline processes, and improve its ability to manage complex production workflows. This project marked one of the first large-scale implementations of 1C:ERP in China, showcasing the system's capabilities in a complex manufacturing environment.
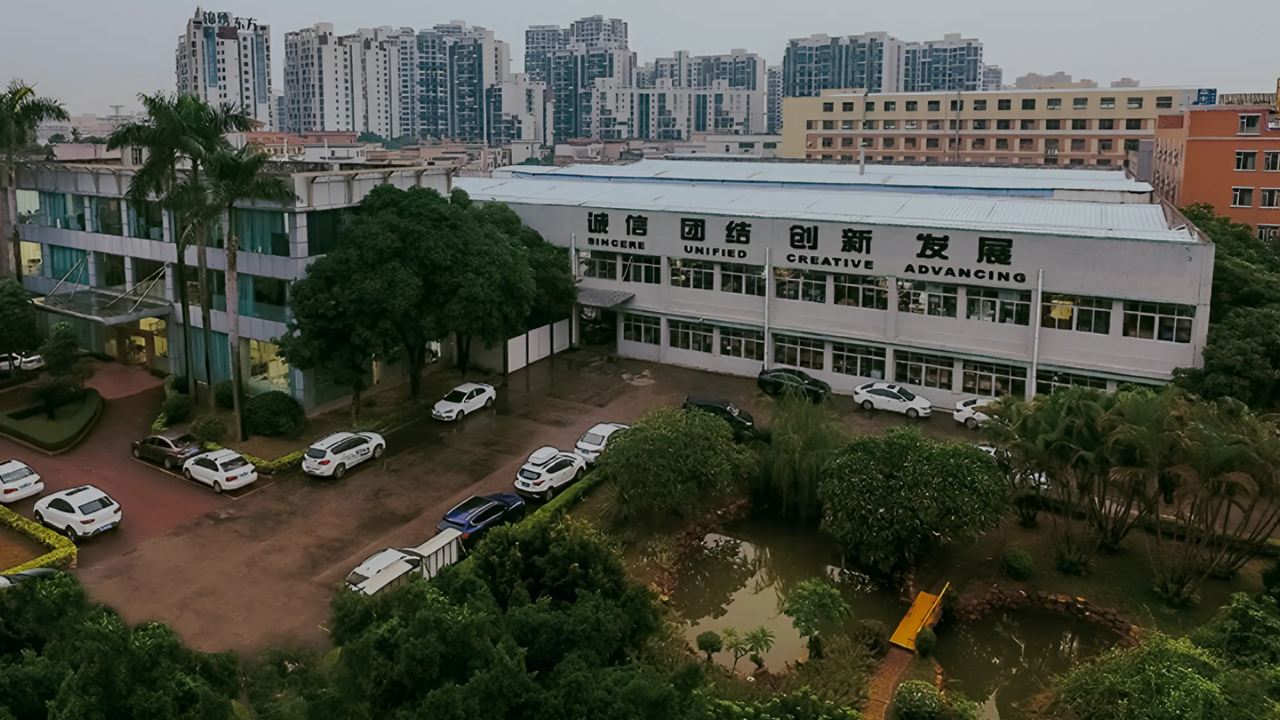
The project involved setting up automated workstations for specific production tasks and customizing a bilingual interface to support both Chinese and Russian languages. This bilingual functionality ensured smooth integration and usability for the Chinese-speaking workforce as well as the Russian-speaking project team. Despite initial concerns about the unfamiliar interface, the Chinese team quickly adapted, fully mastering the new processes within the first week of pilot operations. This successful implementation demonstrated the flexibility and universal applicability of 1C:ERP for production management across various cultural and operational contexts.
About BIG Climatic Manufactory
BIG Climatic Manufactory is a prominent player in China's household and commercial climate equipment market, with a production capacity of over 1.5 million units annually. The company’s extensive product portfolio includes essential appliances for climate control, such as convectors, water heaters, fan heaters, air humidifiers, industrial fans, air purifiers, and hand dryers. With a strong commitment to innovation and quality, BIG Climatic Manufactory has built a reputation for producing reliable and efficient climate solutions that cater to both domestic and commercial sectors.
Key Facts about BIG Climatic Manufactory:
- Location and Facility Size: Based in Guangdong Province in southern China, the company operates within a 20,000-square-meter facility that includes production and storage spaces.
- Workforce: Employs around 350 people, with teams dedicated to various production and support roles.
- Production Capacity: On average, the factory produces 20,000 units across its product range and maintains an overall production capacity of approximately 2 million units per year.
- Full-Cycle Manufacturing: BIG’s manufacturing facility includes five assembly lines, two stamping lines, a painting line, and multiple thermoplastic machines, allowing for a comprehensive, full-cycle production process.
- Research and Development: Emphasizing its commitment to innovation, the company has a dedicated R&D laboratory and holds 57 international patents in industrial design and invention, enabling it to pioneer new climate control solutions.
- Automation: With 70 automated workstations currently in operation, the factory is steadily progressing towards its goal of full production automation, with plans to implement 120 in total.
Choosing 1C:ERP as the ERP Solution
Before implementing 1C:ERP, BIG relied on a basic Chinese ERP system that managed only warehouse operations and limited production processes. As the company grew, it became evident that a more comprehensive solution was necessary to support complex manufacturing workflows and expand capabilities across production planning, inventory management, and quality control.
1C:ERP was selected due to its robust functionalities and flexibility to support BIG’s unique requirements. Here’s why 1C:ERP was the ideal choice:
- Bilingual Interface: With a workforce composed of both Chinese and Russian speakers, it was essential for BIG to have a system that could operate in both languages. 1C:ERP offered this capability, making it easier for the Chinese team and the Russian-speaking project members to collaborate effectively.
- Proven Effectiveness: 1C:ERP’s successful track record with BIG’s key partners further validated its reliability and effectiveness in manufacturing environments, providing the team with confidence in the system's capability to handle complex operational demands.
- Customizable Reporting: With flexible managerial reporting features, 1C:ERP could be customized to meet Chinese national standards while also aligning with familiar Russian accounting practices, ensuring accurate and compliant reporting for cross-border operations.
- Integrated Payroll and HR Management: The 1C:ERP Payroll & HR module streamlined payroll processing and employee compensation management, offering precise and efficient handling of HR tasks across the organization.
Why Raytec DTG was Selected as the Implementation Partner
BIG chose Raytec DTG as its implementation partner due to Raytec’s extensive experience and specialization in ERP solutions for complex manufacturing environments. With over 10 years of experience in 1C:ERP implementations, Raytec DTG has demonstrated expertise in production planning, quality control, and regulatory accounting.
Reasons for Selecting Raytec DTG:
- Extensive Implementation Experience: Raytec DTG’s history of successful ERP implementations, particularly within the manufacturing sector, provided BIG with confidence that they were working with a trusted and skilled partner.
- Industry-Specific Knowledge: Raytec’s team includes certified specialists in key areas such as management accounting, production workflows, and regulatory compliance, all critical for the complex manufacturing operations at BIG.
- Certification and Recognition: As a certified 1C partner, Raytec DTG brought both credibility and proven expertise to the project, helping to ensure a smooth and effective implementation process.
- Focus on Manufacturing Solutions: Raytec’s specialization in manufacturing ERP projects enabled them to offer tailored solutions and insights specific to BIG’s operational requirements.
Project Timeline
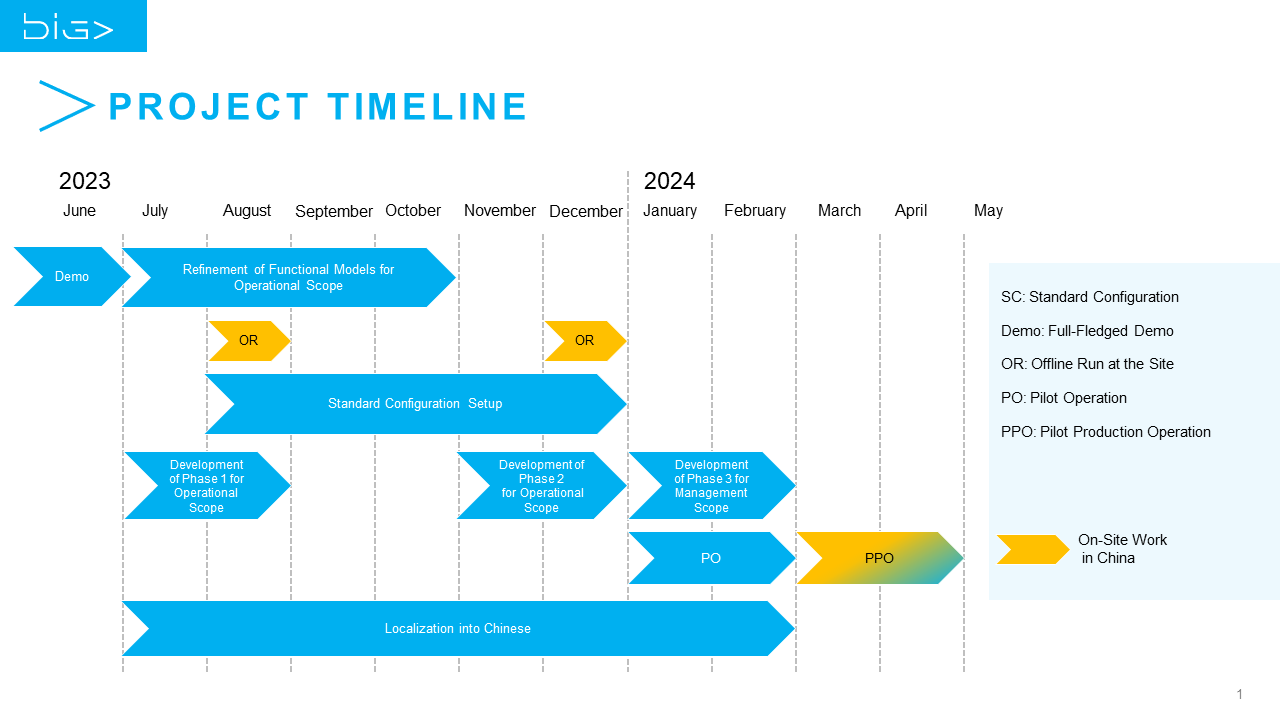
Project Workflow and Key Developments
The implementation project spanned from June 2023 to March 2024, with the primary goal of automating production and optimizing various operational workflows. The project included several crucial components:
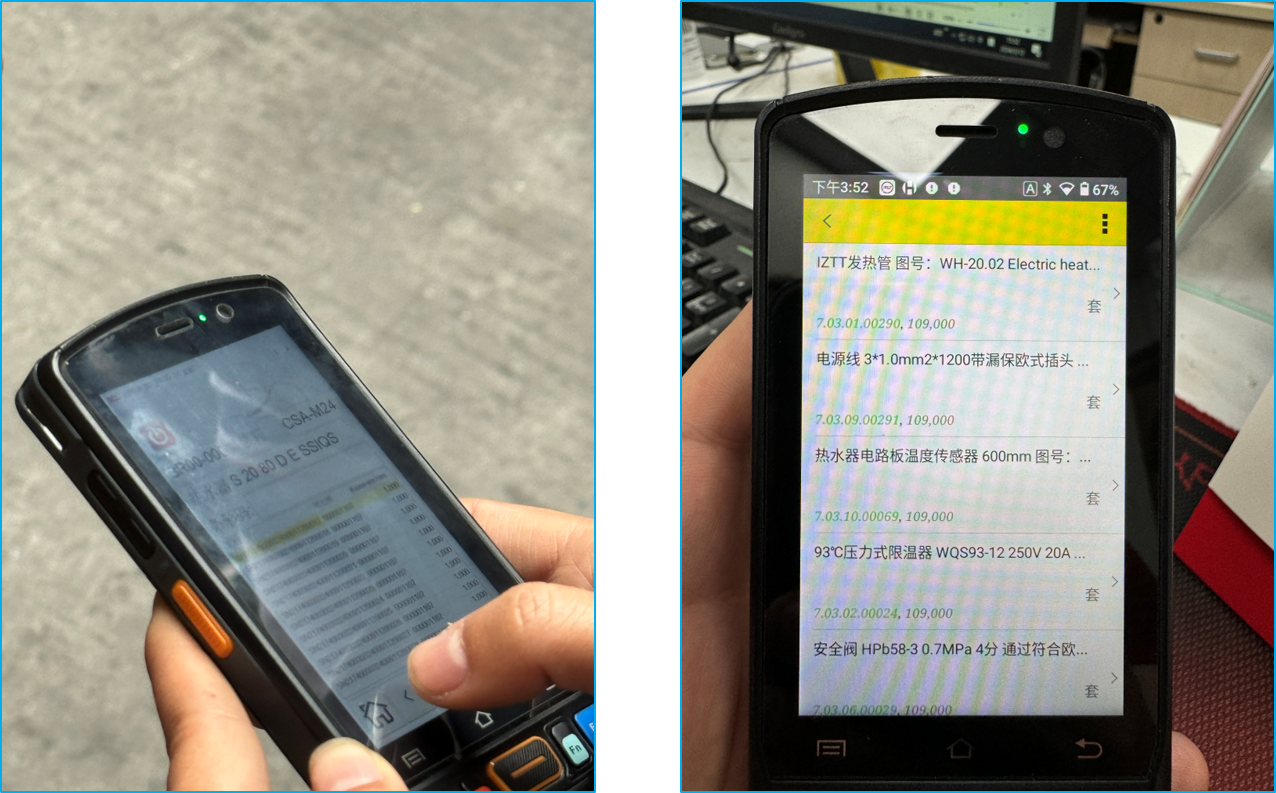
Automation of 70 Production Workstations
One of the project’s main objectives was to automate key production workstations to improve efficiency and accuracy in daily operations. These automated workstations include:
- Information Kiosks: Installed in workshops, these kiosks receive work orders, track production statuses in real time, and eliminate paper-based tracking.
- Conveyor Management: These workstations manage conveyor systems that transport items along production lines, automatically assigning serial numbers and preparing items for dispatch to finished goods storage.
- Warehouse Data Collection: Terminal scanners allow for efficient, cell-based inventory tracking, ensuring high accuracy in inventory management and streamlining warehouse operations. Incoming.
- Material Inspection: Quality control of raw materials is managed through automated inspection processes, helping maintain consistent standards for incoming goods.
- Finished Goods Warehouse: The warehouse automation process includes serial number scanning, palletization, and seamless integration with inventory tracking systems, supporting efficient dispatch to finished goods storage.
Additionally, a dedicated procurement workstation was created to consolidate procurement needs, allowing buyers to access real-time inventory data, order requirements, and production plans. This system automates order calculations and manages material substitutions, ensuring optimized supply chain management.
Interface Localization for the Chinese Market
A crucial step in the project was localizing the 1C: ERP interface to ensure seamless adoption by the Chinese-speaking workforce. Soft Garant, 1C's official partner in China, provided a standard Chinese user experience (UX) package as a foundation.
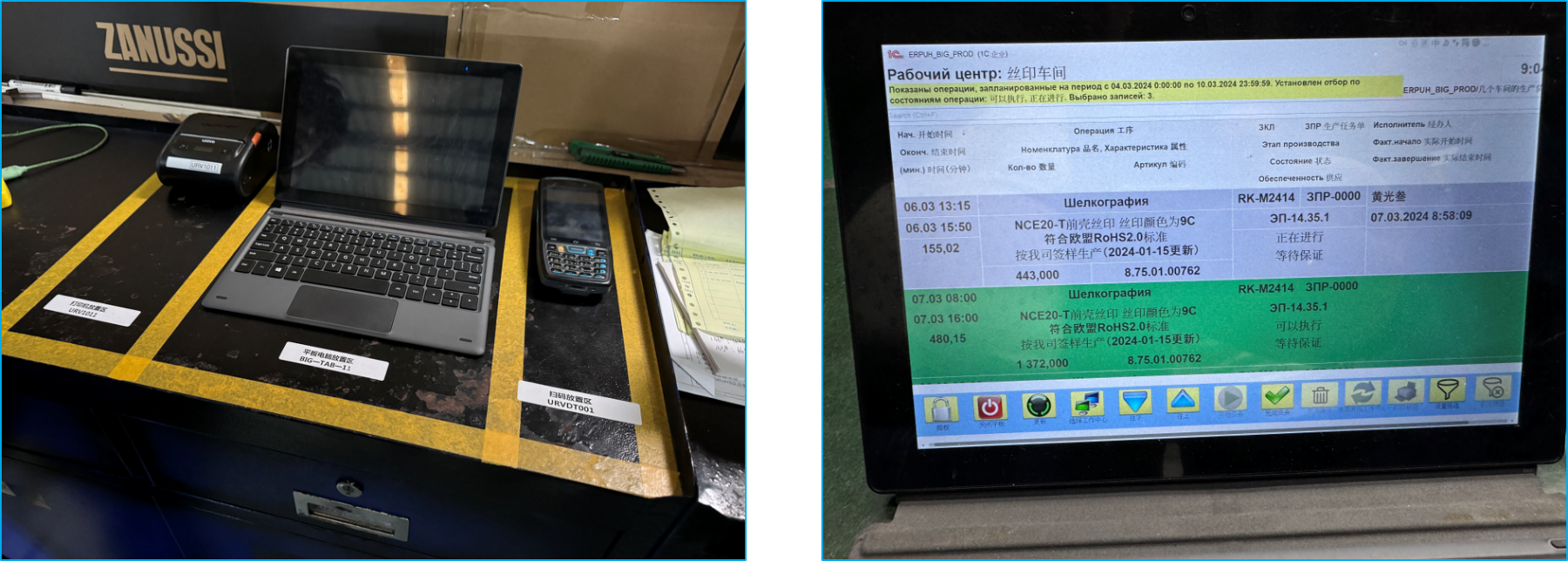
The implementation team then customized this package to align with BIG Climatic Manufactory's specific operational needs and industry requirements. This ensured user-friendliness across all departments and facilitated a smooth transition for employees.
Beyond direct translation, the localization process involved addressing various technical considerations to optimize the interface for Chinese users. This included refining the display of Chinese characters and ensuring all elements were culturally appropriate and intuitive.
The team also recognized that interface localization is an ongoing process. As users interact with the system, they identify areas for further refinement. This continuous improvement approach ensures the 1C:ERP interface remains user-friendly and effective for the Chinese-speaking workforce.
Outcomes and Benefits of the 1C:ERP Implementation
The 1C:ERP implementation delivered significant enhancements to BIG’s operational and production management processes:
- Comprehensive Process Management: The new ERP system supports the entire production workflow, offering centralized control and monitoring for each stage of the manufacturing process.
- Real-Time Production Tracking: With real-time tracking capabilities, production staff can monitor and log outputs immediately, enhancing the company’s ability to fulfill customer orders efficiently.
- Improved Warranty Management: Serial number tracking for finished products allows for more accurate warranty tracking, improving customer service.
- Enhanced Quality Control: By tracking material batches through serial accounting, the company improved its quality management processes.
- Unified Digital Platform: The 1C:ERP platform created a cohesive digital environment, integrating production, warehousing, and inventory management systems into a single, streamlined platform.
Current Operations and Future Expansion Plans
Since implementation, BIG has used 1C:ERP to manage master data, including production specifications, medium-term and operational planning, and warehouse logistics. Additionally, the ERP system supports a newly developed quality management module, reinforcing the company’s commitment to excellence.
Future Automation Initiatives
As BIG transitions into a more advanced phase of ERP usage, they plan to expand automation into additional management areas. Key priorities include:
- Time Tracking and Payroll: Automated systems will be implemented to record working hours precisely, allowing for efficient payroll management.
- Treasury Management: The treasury management module will enhance financial oversight, helping the company manage its resources effectively.
- Income and Expense Tracking: Automation in income and expense tracking will ensure accuracy in financial reporting, providing critical insights into operational costs and profitability.
- Advanced Costing Mechanisms: Comprehensive costing systems will enable precise calculations of production costs, supporting informed decision-making and cost optimization.
These initiatives demonstrate BIG’s commitment to continuous improvement, as they leverage 1C:ERP to support growth, efficiency, and industry leadership.