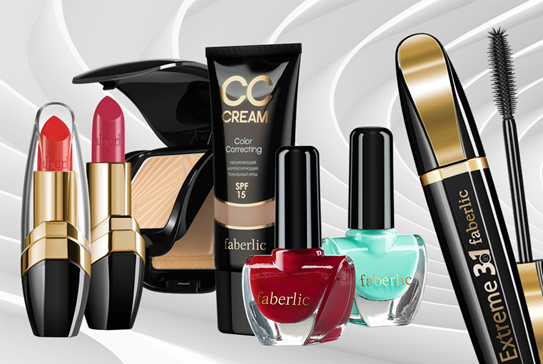
Faberlic is the largest Russian company in the cosmetics market, a manufacturer of unique oxygen cosmetic products. Faberlic’s production is based on European quality standards and is fitted up with the high-tech and eco-friendly equipment, automatic lines for the production, packing and packaging of cosmetic items.
In 2003 the company internationalized its business, nowadays Faberlic has a presence in 24 countries. The firm has up to 30 patents and is included in the rating of “Top 100 largest cosmetics companies of the world.”
Earlier, the Faberlic enterprise used an information system of the ERP type of a foreign supplier to execute production accounting. However, the central ERP system was developed on the basis of the domestic 1C:ERP software product.
A general examination of the production accounting system detected the following drawbacks:
-
a lack of standardized production processes and a unified information space to carry out efficient production accounting;
-
execution of most of the production operations needed manual control;
-
the imperfection of the production planning stage;
-
a lack of information about current and correct stock balances of raw materials, semi-finished and finished goods;
-
a lack of mechanisms for plan/fact analysis and efficient production control.
The main project goals were to standardize accounting procedures and automate production management business processes.
Project tasks
1) decrease the influence of the human factor on the implementation of key production management processes;
2) ensure automatic data collection analysis and optimization of the company’s supply chains;
3) make it possible to carry out thorough quality control at all production stages.
A team of specialists from the Borlas company, an official 1C partner, was responsible for the system development and implementation.
Project uniqueness
The project team developed a paperless production concept using data collection terminals which helps:
-
ensure complete traceability of material consumption (compliance with the GMP standard);
-
automatically assign employees for operations to keep up with the quality control requirements;
-
reduce the time needed for shipment of cosmetics to the end customer due to the efficiency of organizing partial production output.
Solution architecture
The implemented information system for production planning and management is developed on the 1C:ERP software product basis. All the fundamental and auxiliary business processes of production planning and accounting were automated as well.
Project results
The creation of the production management information system allowed the Faberlic company to comprehensively replace the previously used IT system, as well as automate business processes that were not previously included in the automation framework. The new software made it possible to:
-
decrease the influence of the human factor on the implementation of key production management processes;
-
reduce the time needed for shipment of cosmetics to the end customer due to increased efficiency of business operation registration and enhanced production planning quality;
-
ensure complete traceability of material consumption when manufacturing cosmetic articles (compliance with the GMP standard).