Glass processing company «GlassTechnology» has automated production management using the 1C:ERP Enterprise Management solution.
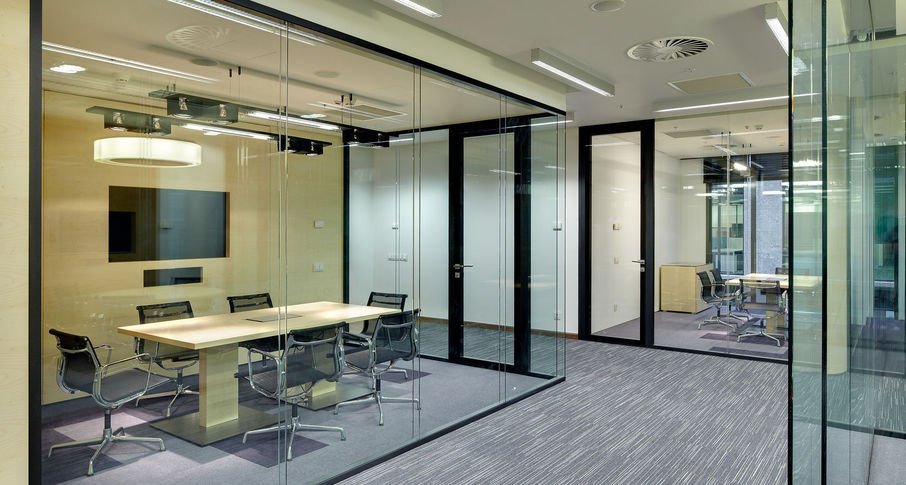
The ERP system helped to organize production planning for customer orders, taking into account the implementation of each production stage. The specifications calculation for complex custom product configurations has been accelerated.
Accurate accounting of raw materials transferred for processing and semi-finished products received from contractors has been established. The control over each stage of the technological process was strength.
Also, the exact calculation of the actual production cost has been ensured. The management now has the opportunity to monitor the work of units in real-time. The fulfillment of production orders accelerated by a factor of 1.5.
"GlassTechnology" LLC is a glass processing company; since 2010, it has been part of the Nayada group. It specializes in the production of various types of glass of high quality – from the usual single-layer version to complex solutions with individual design.
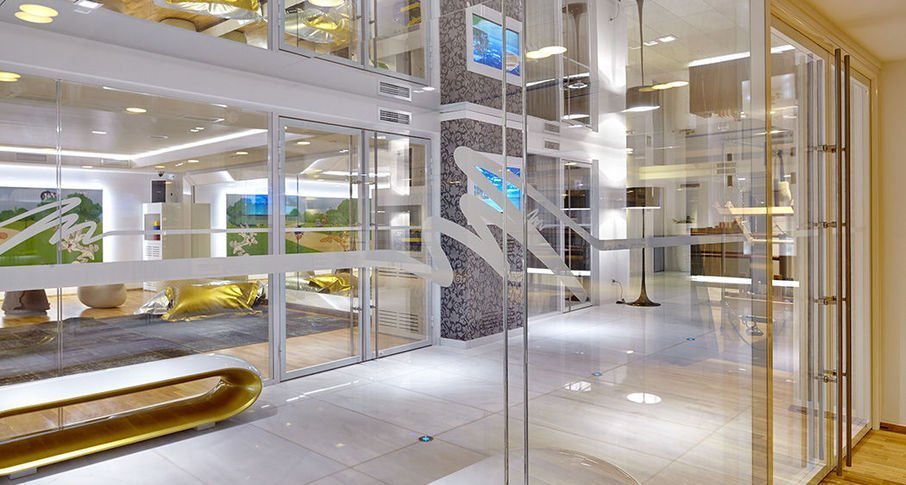
Every day the company receives about 200 orders for the products' production. Upon receipt of each order, it is necessary to quickly evaluate the possibility of its execution within the period desired by the client, form a specification, and calculate raw materials.
The company outsources contractors for the production of some semi-finished products, so it is necessary to control the transfer of raw materials to the side and the return of finished semi-finished products from processing.
Previously, the company did not have a system for sales planning, procurement, and provision of warehouses. Production was planned in spreadsheets and no more than a week in advance.
Coordination of cost, production time, dates of shipment of orders was carried out on paper. Frequently, there were errors in the formation of specifications. It was difficult to control the flow of orders through the process chain.
Time tables were kept manually, which made it impossible to estimate the workload of employees. It was required 3 to 7 working days to obtain information about the state of the company's affairs to date.
The company needed an information system that would standardize procurement, warehouse, and sales management, organize operational production planning for customer orders.
It was necessary to ensure accurate accounting of raw materials, materials, and semi-finished products, accelerate the formation of production specifications, and tighten control over each stage of the orders' execution.
Besides, it was necessary to automate regulated accounting and ensure that management reporting on the work of units in real-time was obtained.
To address the issues, the system "1C: ERP Enterprise Management" was chosen. The implementation partner was the "Institute of Standard Solutions - Production" company (LLC "ITRP").
During the project, 120 workplaces were automated, the system includes company management, dealership managers, representative offices, warehouse employees, delivery managers, planning and dispatching department employees, logistics department employees, technologists, production dispatchers, and accounting department.
Key project outcomes:
All of the enterprise's critical tasks — production, procurement, processing, product release, individual customer orders, sales, etc. — are now regulated and automated.
Data collection terminals (TSD) are connected to the system, which is used to register the beginning and completion of production operations, accounting of materials, and marriage at each stage of the technological process. The passage of semi-finished products through the process chain has been accelerated. Errors during production operations have been excluded.
Real-time information about each stage of the orders' production execution is now available. Sales managers no longer need to contact the employees of the planning and dispatching department and employees of production units to obtain information on the orders' readiness. Information on the current status of each order at any time is available in the system. Sales staff can quickly identify the causes of possible delays in the execution of orders, take measures to prevent deadlines, or, if necessary, coordinate new delivery dates with customers.
An accurate calculation of the actual cost of production has been provided. It helps to control the cost of production and rationally manage the profitability of orders.
Besides, the system promptly generates detailed reports on the current performance of units.
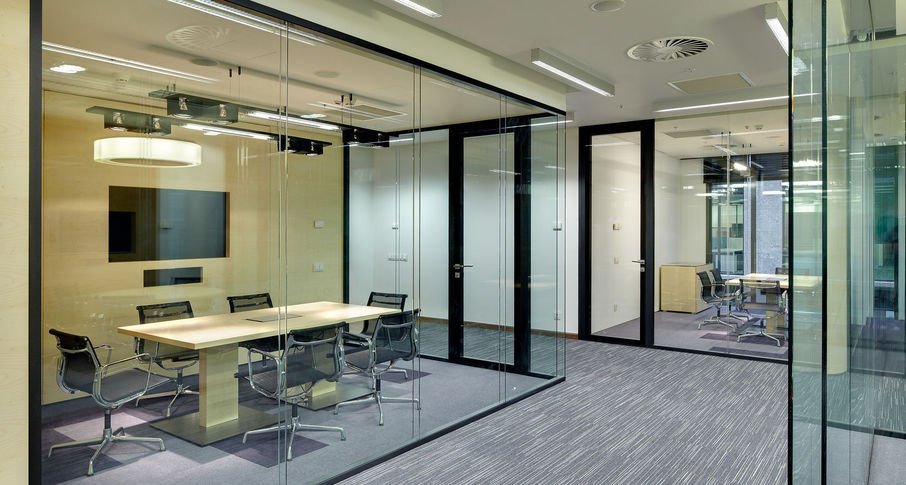
The ERP system helped to organize production planning for customer orders, taking into account the implementation of each production stage. The specifications calculation for complex custom product configurations has been accelerated.
Accurate accounting of raw materials transferred for processing and semi-finished products received from contractors has been established. The control over each stage of the technological process was strength.
Also, the exact calculation of the actual production cost has been ensured. The management now has the opportunity to monitor the work of units in real-time. The fulfillment of production orders accelerated by a factor of 1.5.
"GlassTechnology" LLC is a glass processing company; since 2010, it has been part of the Nayada group. It specializes in the production of various types of glass of high quality – from the usual single-layer version to complex solutions with individual design.
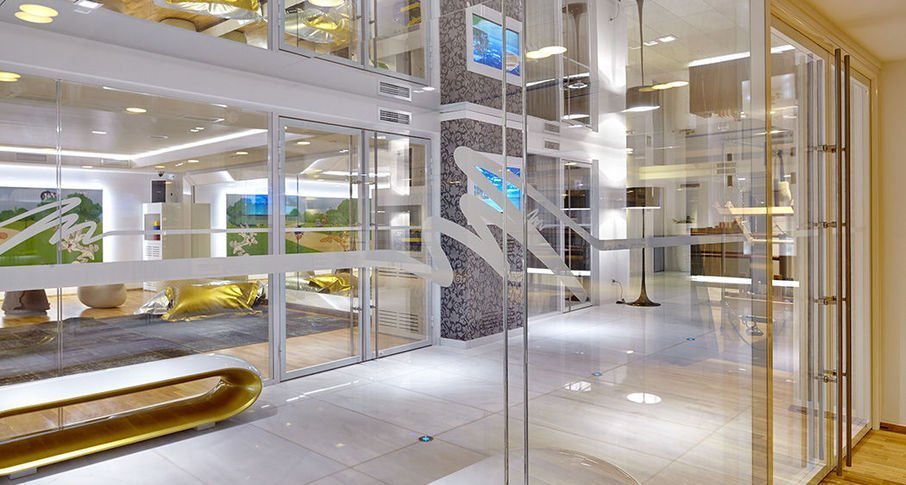
Every day the company receives about 200 orders for the products' production. Upon receipt of each order, it is necessary to quickly evaluate the possibility of its execution within the period desired by the client, form a specification, and calculate raw materials.
The company outsources contractors for the production of some semi-finished products, so it is necessary to control the transfer of raw materials to the side and the return of finished semi-finished products from processing.
Previously, the company did not have a system for sales planning, procurement, and provision of warehouses. Production was planned in spreadsheets and no more than a week in advance.
Coordination of cost, production time, dates of shipment of orders was carried out on paper. Frequently, there were errors in the formation of specifications. It was difficult to control the flow of orders through the process chain.
Time tables were kept manually, which made it impossible to estimate the workload of employees. It was required 3 to 7 working days to obtain information about the state of the company's affairs to date.
The company needed an information system that would standardize procurement, warehouse, and sales management, organize operational production planning for customer orders.
It was necessary to ensure accurate accounting of raw materials, materials, and semi-finished products, accelerate the formation of production specifications, and tighten control over each stage of the orders' execution.
Besides, it was necessary to automate regulated accounting and ensure that management reporting on the work of units in real-time was obtained.
To address the issues, the system "1C: ERP Enterprise Management" was chosen. The implementation partner was the "Institute of Standard Solutions - Production" company (LLC "ITRP").
During the project, 120 workplaces were automated, the system includes company management, dealership managers, representative offices, warehouse employees, delivery managers, planning and dispatching department employees, logistics department employees, technologists, production dispatchers, and accounting department.
Key project outcomes:
All of the enterprise's critical tasks — production, procurement, processing, product release, individual customer orders, sales, etc. — are now regulated and automated.
Data collection terminals (TSD) are connected to the system, which is used to register the beginning and completion of production operations, accounting of materials, and marriage at each stage of the technological process. The passage of semi-finished products through the process chain has been accelerated. Errors during production operations have been excluded.
Real-time information about each stage of the orders' production execution is now available. Sales managers no longer need to contact the employees of the planning and dispatching department and employees of production units to obtain information on the orders' readiness. Information on the current status of each order at any time is available in the system. Sales staff can quickly identify the causes of possible delays in the execution of orders, take measures to prevent deadlines, or, if necessary, coordinate new delivery dates with customers.
An accurate calculation of the actual cost of production has been provided. It helps to control the cost of production and rationally manage the profitability of orders.
Besides, the system promptly generates detailed reports on the current performance of units.