MCS Coca-Cola
MCS Coca-Cola is a part of the MCS Group holding, which specializes in the field of information, communications, construction, real estate, industry, and infrastructure. It implements large-scale projects aimed at the global development of Mongolia.
MCS Coca-Cola has been producing world-class drinks since 2002. Today it produces 140 types of products of 9 brands. The number of employees is more than 860.
With the growth of turnover, the requirements for depth and accuracy of operational planning and production control increased and the company faced a number of problems that could not be resolved within the framework of existing systems.
Before the implementation of the project:
-
Most parts of the internal processes were carried out manually.
-
Information about the presence of product balances in the system for receiving customer orders was not transmitted promptly, and sales representatives often placed orders for missing positions.
-
Automation systems for collecting data on enterprise activities, reporting, and planning were absent or did not meet current business requirements.
-
Most of the accounting work was carried out in Microsoft Excel spreadsheets.
-
Processing and evaluating information from different departments took more than one working day and required significant labor costs.
Goals and objectives of the project
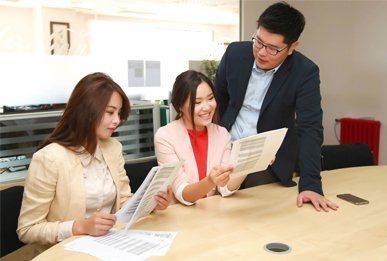
The main goal of the project was to create a common unified information system that will provide management and regulated accounting, automation of business processes of production, repairs, procurement, and storage for all departments of the enterprise.
The creation of the system was aimed to solve the following problems:
-
quick access to adequate information about the balances and movement of inventory items;
-
reduction of labor costs for calculating the planned and actual cost of finished products;
-
reduction of operators' labor costs when posting payments from customers;
-
operational monitoring of indicators of economic efficiency of the enterprise.
Solution architecture and project scope
The unified information system of the enterprise is built on the basis of the 1C:ERP Enterprise Management 2 solution, version 2.4, which covers the needs for automation of the main operational accounting units. To automate regulated accounting, 1C partner decided to install 1C:Accounting CORP 3.0 - a customized solution for Mongolia with a special block International Financial Accounting. They developed exchange rules between configurations from scratch and implemented them using the Data Conversion 2.0 configuration.
To exchange data with the Yukon database (a mobile application for automating the work of sales representatives), they developed exchange processing through an intermediate database (SMTExchange).
1C:ERP Enterprise Management 2 was implemented in all divisions of the company for 102 workplaces.
6 days a week the company completes about 2-3 thousand orders. All the information downloads from the system for sales representatives in 1C:ERP Enterprise Management 2. Information about payments, balances of goods, and finished products downloads at the same time. Then the sales are uploaded to the accounting system.
Features and the uniqueness of the project
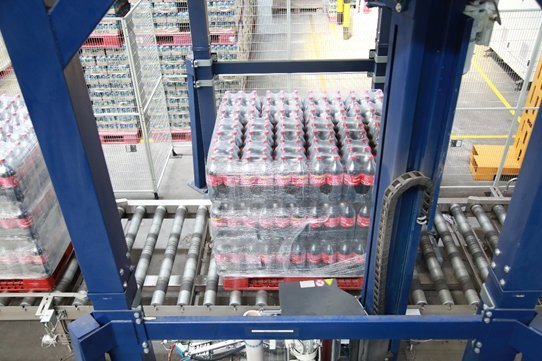
MCS Coca-Cola is part of the largest Mongolian holding MCS, which uses a unified chart of accounts for international accounting. Therefore, for maintaining regulated accounting, they moved the mechanism of the financial international accounting unit from 1C:ERP Enterprise Management to 1C:Accounting.
All units involved in automation were significantly redesigned to meet customer needs.
For example, one of the features of the project is the registration of multi-turn containers: MCS Coca-Cola delivers finished products in glass bottles, which are containers. When returning to the factory, the bottles are washed and stored in boxes, which are also multi-turn containers. There are several formats for transferring containers to customers. That is why it is necessary to keep track of containers for which they developed the “Container” workstation. Moreover, in regulated accounting, it is reflected as the main means.
1C Partner implemented an automatic exchange with the system used by sales representatives: loading orders, unloading reference information, information on mutual settlements with customers, and sales data.
They developed an algorithm for planning and automatic control of repair work for a year, indicating the performers and materials.
It was developed as an algorithm for the automatic distribution of orders by machines. They adapted the workstation "Delivery" for the selection and grouping of orders by various filters.
It was developed an algorithm for automatic reforming of production plans, taking into account the congestion of lines during the “season” and adjustments for the actual implementation of the plan for the last month.
The uniqueness of the project: The project team managed to put the systems into commercial operation in record time (6 months) without interrupting the work of units. All blocks of operational and regulated accounting were launched on January 1, 2020, with the simultaneous shutdown of old systems.
Project results
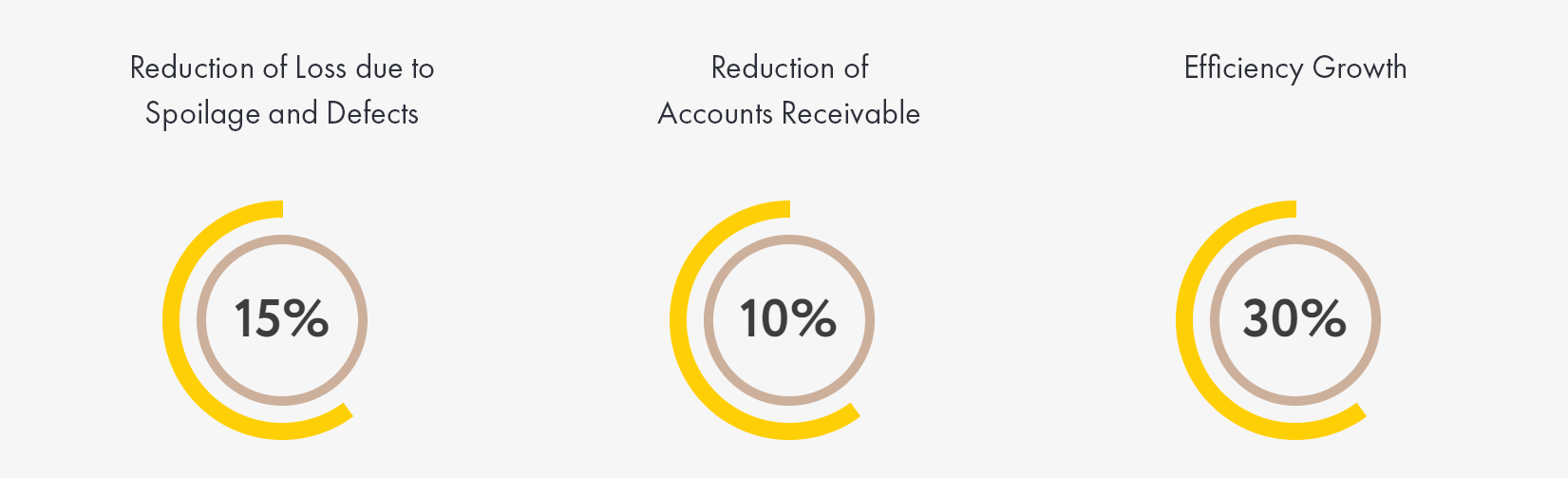
-
A unified information system at the enterprise, due to which it is expected an increase in the accuracy of records of the production process of 70%.
-
A common information space for the all departments in the online mode, which removes the double reflection of the same operations, redistributes the responsibilities of employees and uses the human resource by about 20% more efficiently.
-
Organized address storage of products. The system reflects all the necessary information about the product. As a result, the increased company expects a 15% reduction in the loss of goods from spoilage and marriage.
-
Up-to-date information on stock balances and current production orders, which allows the company to improve the quality of planning and make management decisions more quickly.
-
The accuracy of the cost budget calculation has increased due to a more detailed distribution of indirect costs for the output product. The accuracy of reflecting the actual cost in regulated accounting has increased due to the fact that the difference between the planned and actual cost goes to a separate account and was not allocated on the production cost. Now all expenses are allocated on the actual cost.
-
Accounting and finance departments receive current operational data on receivables and payables, which allows carrying out quality control over the status of settlements with counterparties. The planned reduction in receivables is 10%.
-
The information system allows users to send data to the tax authorities directly from the system.
- Monitoring of employee performance improvement. The expected increase in labor productivity is 30%.